In mechanical and plant engineering, the customer-centred improvement of delivery speed and quality is a key objective, whereas resource efficiency has been less of a focus so far. The project “RePARE” aims to complement measures such as preventive maintenance and the high safety stock of spare parts with additive repair procedures, thus enabling the systematic regeneration of spare parts.

Additive repair in mechanical and plant engineering
The competitive pressure in the mechanical and plant engineering industry leads to new strategies to ensure differentiation from global competition. One strategy for enhancing economic and ecological sustainability is to extend the life cycle of machines by converting, replacing or upgrading components. In order to contribute to this, the project is investigating the remanufacturing of partially worn spare parts using additive manufacturing processes such as Selective Laser Beam Melting or Laser Metal Deposition in the sense of additive repair.
With the help of an economic-technical framework, an evaluation is made of which components are suitable for remanufacturing. From a business management point of view, holistic service concepts for the use of additive repair are defined and, by means of parameters, the reparability is evaluated in terms of a rebuild-or-replace decision. The consideration of life cycle assessment extends the view of sustainability.
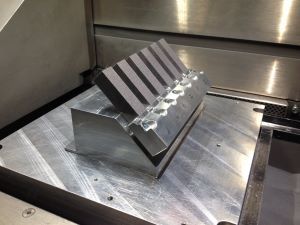
The Potentials
The use of additive manufacturing for the remanufacturing of spare parts is associated with various potentials and challenges, which will be investigated and discussed in the project, also by tests using demonstrator components. On the one hand, the costs incurred by manufacturers, such as spare parts storage and logistics, and customers, such as downtime costs, can be minimized and the life cycle of components extended. On the other hand, there is the challenge of carrying out downstream activities such as installation and removal as well as quality assurance of the spare part with regard to warranty and liability issues. Since the market for additive manufacturing is highly dynamic, the project team also looks beyond the research period in the context of a scenario analysis, for example to anticipate developments in production unit costs.
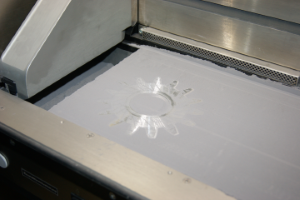
Results (Status June 2022)
In the course of the project so far, potential applications for additive repair and refurbishment have already been identified, even beyond high-priced capital goods. Furthermore, decision variables for the selection of suitable components have been determined. The specific repair strategy in the event of a component defect depends on various factors, such as the damage and its orientation in the component, so that the necessary expert knowledge was collected and transferred in a structured manner into a design catalog. The embedding of additive repair processes into existing after-sales structures requires the configuration of customer-specific solution offerings, which were addressed by means of a service architecture. For this purpose, various assistance systems were developed: A process support system allows even non-experts to carry out the installation or removal of the component. A configurator for process chains of additive manufacturing and a cutting plane generator can be used to provide the expert knowledge required to repair a component, thus achieving spatial flexibility in after-sales. A process cost calculator and an optimization model for planning warehouse and manufacturing locations support the operational design by identifying an optimal solution for supplying spare parts from a conventional warehouse or via mobile repair centers on the basis of economic criteria.
Furthermore, the first demonstrator components have already been successfully repaired and subjected to load tests in order to also test their practical application. The knowledge gained is currently being used to evaluate the developed modules and to carry out the life cycle assessment of the additive repair. In this way, the project contributes to replacing material supply chains with virtual data transfer and to supporting customers worldwide in maintenance, remanufacuring and repurposing.
Consortium and results
In RePARE, scientists from the German Research Center for Artificial Intelligence (DFKI) are working together with engineers from the Institute for Product Development and Engineering Design (iPeG) at Leibniz Universität Hannover. The DFKI team will explore the potential that arises from the business model and the circular economy and provide a summarizing framework by developing a complete system for the systematic integration of additive repair scenarios right through to the service processes. The IPeG investigates different repair strategies for plant engineering components, executes practical tests and subsequently validates the regenerated components. The results are incorporated into an assistance system that supports designers in the design and planning of repair tasks.
From industry, the researchers receive support from DMG Mori Spare Parts GmbH and Windmöller & Hölscher KG. The industrial partners are supporting the project by collecting and classifying wear mechanisms and comparing manufacturing technologies for the recirculation of components. Furthermore, from a practical point of view, questions regarding the type or mechanism of damage, suitable materials and integration into the value chain are of interest. Based on these questions, a quantification of the procedures with regard to processes, life cycle assessment and proportionality can be carried out.
Publications
Project flyer of the funding measure (German / English) (March 2021)
The project flyers offer an insight into the contents and goals of the ReziProK projects and present first results in each case.
Project sheets of the funding measure (German) (September 2019)
The project sheets provide a brief overview of the individual projects and their goals.
Contributions to the ReziProK Transfer Conference in June 2022
Poster (German) (June 2022)
Presentation (German) (June 2022)
Contributions to the ReziProK Kick-off event in December 2019
Poster - in German (December 2019)
Presentation - in German (December 2019)
Picture credits: IPeG, Leibniz Universität Hannover