In the foundry and steel industry, around 45 percent of the raw material requirements are already covered by secondary raw materials. This proportion should and can be increased. A prerequisite is that the smelters know the exact composition of available scrap types and can procure them in a targeted manner. For this reason, the "OptiRoDig" project aims to develop a digital network system that enables data exchange between the recycling industry and steelworks for optimized melting processes.
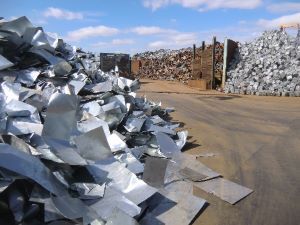
Metal recycling with potential
Metal scrap is produced in large quantities as waste from metal processing, e.g. chips, punching waste, material residues. Usually their exact composition and any impurities they may contain, e.g. oils, are not known exactly. However, this information is a prerequisite for the smelters to be able to use specific scrap qualities for the production of a certain alloy without having to add expensive alloy surcharges.
Foundries and steelworks or smelters want to purchase the raw materials suitable for their melting processes in a targeted and cost-effective manner. Today's common procedure - inquiry, quotation, order - is time and personnel consuming. In addition, the desired material data is often not available in a timely manner.
In the course of OptiRoDig, a digital network system is to be developed between the recycling industry and the smelters. In this system, extensive analysis data of available secondary raw materials - metal scrap - will be provided. This database should enable the smelting works to procure suitable raw materials, to optimise their melting processes and thus to use higher proportions of secondary raw materials in a targeted manner.
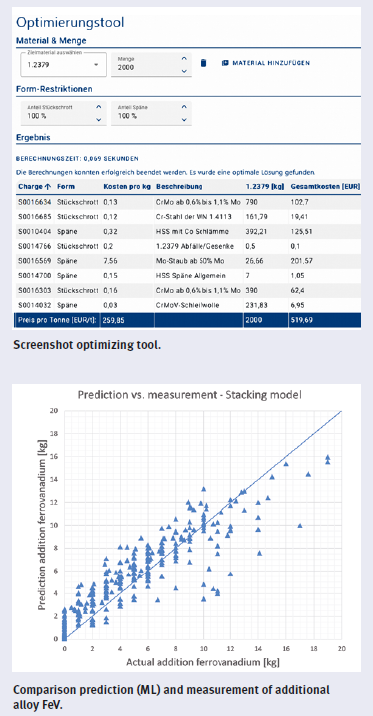
Digitisation and networking
For interactive data exchange and automated process optimization in the melting plants, both the data to be recorded and various software tools must be developed and coordinated. In OptiRoDig an innovative digital system is to be developed for this purpose, via which the raw material data and process requirements are made available digitally to the participants along the process chain through digitisation, networking, defined interfaces and data formats in such a way that these can be taken directly from the planning software and evaluated using mathematical methods. For this purpose, comprehensive analysis coordinated between the partners is required. After completion of the development phase, the digital system is to be made available to other companies within the framework of a cloud solution.
Results (Status June 2022)
In the cloud-based web application created for the project, it is possible to optimise the melt composition in terms of costs with a simplex algorithm. These optimisations can be supplemented as needed with further boundaries, for example related to the shape and ratio (proportion of turnings / piece scrap) of the available scrap.
Further melting tests were carried out in the furnace of our project partner's foundry. The resulting data was fed into the machine learning (ML) software to model optimisations for cost and energy consumption. The ML models are integrated into the cloud application. An overall optimisation can be made for the metallurgical interactions in the melt and total costs.
For the scrap characterisation, the use of analysers and in-house process optimisation has advanced the classification of physical and chemical attributes as a contribution to increase resource efficiency.
Consolidation of competences
The joint project OptiRoDig brings together the main players in the supply chain between the points where metal waste is generated and steel production. These are supplemented by the know-how of university institutes.
The project coordinator is MAI Metal Alloy Impex GmbH, a wholly owned subsidiary in the RHM Group, based in Mülheim. As a scrap trading company, MAI specialises in the sector of high-quality steel alloys and related metal alloys with rare elements such as tungsten, chromium, valadium, cobalt, nickel, titanium, etc.
The smelting works of Friedr. Lohmann GmbH, based in Witten, act as representatives of the "OptiRoDig" network. In their two steelworks, high-speed, tool and special steels are produced as well as highly wear-resistant and heat-resistant castings.
The Institute of Metal Technologies at the University of Duisburg-Essen (UDE) and the University of Applied Sciences Kempten have many years of expertise in the fields of process optimisation, database systems, static evaluation and predictive manufacturing.
The partners MAI and Friedr. Lohmann benefit from the results by optimizing their processes and the application-oriented evaluation of raw materials. The university institutes can test and optimize developed models and algorithms in operational practice. In the second project phase of "OptiRoDig", the data exchange is then to be made accessible to other companies in the recycling industry as well as the foundry and steel industry.
Publikationen
- Tonnius, A. & Kaufmann, T. (2021). "Datenbasierte Optimierungsverfahren. Giesserei, die Zeitschrift für Technik, Innovation und Management"
- Kaufmann, T. & Chen, S. (2021). Development of data-driven machine learning models for the pre-diction of casting surface defects. Metals, special issue: Optimizing Techniques and Understanding in Casting Processes
- Chen, S. & Kaufmann, T. (2022). "Datenbasierte Verfahren zur Steigerung der Energieeffizienz beim induktiven Schmelzen. stahl. - Das Magazin für die Stahlindustrie"
- Jonas, C., Lohmann-Voss, F. & Kaufmann, T. (2022). "Datenbasierte Methoden zur Steigerung der Energieeffizienz. Giesserei, die Zeitschrift für Technik, Innovation und Management"
- Kaufmann, T., Chen, S. et. al. (2023). “Applied machine learning and optimization in steel melting”. heat processing - International Magazine for Industrial Furnaces, Heat Treatment & Equipment, 02/2023
Project flyer of the funding measure (German / English) (March 2021)
The project flyers offer an insight into the contents and goals of the ReziProK projects and present first results in each case.
Project sheets of the funding measure (German) (August 2019)
The project sheets provide a brief overview of the individual projects and their goals.
Contributions to the ReziProK Transfer Conference in June 2022
Poster (German) (June 2022)
Presentation (German) (June 2022)
Contributions to the ReziProK Kick-off event in December 2019
Presentation - in German (December 2019)
Picture credits:Friedr. Lohmann GmbH Universität Duisberg-Essen Hochschule für angewandte Wissenschaften Kempten