Components, such as bearings, springs e.g. in machines, are often replaced significantly before they reach the technically possible service life and are sent too early to material recycling or disposal. Using selected applications, the partners in the consortium want to show that a decentralised condition assessment with a prognosis of the remaining service life can lead to longer use and thus make a contribution to improved resource efficiency.
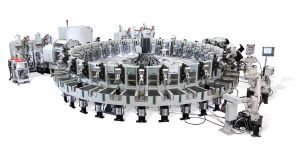
Sustainability instead of short-term effects
We have defined two Use-Cases for the project “LongLife”. On the one hand, the drive spindle of an injection unit from a shoe machine and on the other hand mechanical components of an industrial high-speed roll-up door. Components in technical systems, such as bearings, drive belts and springs are regularly replaced according to a maintenance schedule, although in some cases they could be kept in use much longer. One reason for this is often the uncertainty regarding the actual condition of the components and their expectable remaining service life, because such information cannot be obtained with existing means and data or because the cost-benefit ratio is unacceptable. A further barrier is that the business models of the involved companies are often not geared to such extended use of the components. For example, manufacturer´s main interest is usually to sell new products rather than supporting the re-use of used products, not least due to warranty issues and margins. As a result, this leads to unnecessary costs and burdens the environment through increased resource consumption.
Increased certainty regarding the remaining service life
The partners of the “LongLife” consortium want to remove barriers for a longer use of technical components and thus contribute to a significant saving of resources. This is to be achieved by combining technical and business management elements. On the one hand, methods and tools will be developed for the most reliable possible prognosis of the remaining service life of used technical components. On the other hand, innovative reference business models are to be developed that build on these results and provide tangible benefits for all partners that are involved in the extended use of the components.
The application partners´ motivation is to quickly obtain an assessment of the condition of the considered components when problems occur with the overall system. Based on this, it can then be decided whether the component has to be replaced or still can be used for a longer period of time so that, for example, an extra on-site service can be avoided, especially when technicians have to travel abroad. As an additional service, the users of the components should be provided with information regarding the options for emergency operation until the next regular service.
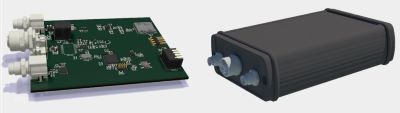
Results (Status June 2022)
The wear-afflicted components on a high-speed roller door and an injection unit of a shoe machine were supplemented with sensors so that test series for condition monitoring could be started. Challenges arose from data technology, since on the one hand existing data from the control system (PDA) or drive had to be combined with data from the sensor box developed in the project. The measured values from the drives and the additional sensors had to be merged, whereby the network of the respective users in the environment of the plants was used for the data transport. This limited the amount of data that could be transferred, and data pre-processing had to be performed at the sensor node to maintain data reduction while preserving data quality for subsequent analysis.
The theoretical model for the condition diagnosis of components was further developed. The basic principles were compiled from technical literature and expert discussions and taken into account in the model. The parameters derived from this for condition determination are not consistently recorded directly. Accordingly, other measured variables were investigated that indirectly indicate the required parameters. For example, for the physical parameter "torque", the power consumption of the machines is measured.
The core idea of the model is to compare the target and actual curves over the component service life. If known target curves of the recorded parameters are available, the component wear is determined on the basis of the actual curves and the determined deviations. For example, a known course of the relaxation of a tension spring is used to check whether the spring rate has changed. Furthermore, critical value ranges are determined for selected measured variables. Values that fall within this range are recorded and the damage caused by them is determined according to the quantity of data. An example of this is the critical range of relative humidity (>60%), in which the corrosion load increases sharply. Ultimately, with the help of anomaly detection, a possible misbehavior of the monitored components is to be detected.
In a long-term test on the roller shutter, changes in the recorded measured variables are currently being identified during the analysis of the recorded data. Among other things, the spring elongation could be identified from the course of the torque at the drive. As the cycle state (closing and opening operations) increases, the applied torque of the drive decreases and the cause of this is the material fatigue of the spring and the associated change in the spring rate. Other hypotheses, such as the change in speed acceleration with progressive component wear, were rejected because no change was discernible here. Visual condition monitoring was carried out for the belt and timing belt components during the long-term test. Increasing fraying and discoloration were detected for the belt. In the case of the toothed belt, indentation edges on the teeth were detected. In addition to the changes described, the cycle status of the individual components is available, so that a condition diagnosis is carried out on the basis of the known target curves.
Parallel to the roller shutter, tests were carried out on the drive spindle of the shoe machine at various companies. Defined conditions, such as operation with a dirty mixing screw and mixing chamber, could be tested in different combinations. The analysis of the measurement data showed that the states can be recognized and distinguished with the help of the calculated root mean square (RMS). This mathematical mean is calculated from the recorded alternating acceleration and transmitted by the sensor box. Using these measured variables, the process sequence can also be interpreted and narrowed down in terms of time. Furthermore, the recorded operating data of the system provide information about the load duration of the drive spindle in the selected period. For this purpose, the shot counter is read out, which counts the load cycles run.
As in the case of the application described above, a comparison between the current and new condition is necessary for the condition diagnosis. Information is provided by the collected measurement data, which is retrieved at the known installation time of the drive spindle. Based on the known installation time of the drive spindle and the load duration described in advance, a comparison can be made with regard to the calculated basic rating life. The operating temperature, which is also recorded, has a further influence on the condition of the components. The permissible maximum value is determined by the closed rolling bearings in the drive spindle, which are provided with solid lubrication. Furthermore, with the help of the recorded torque, the load on the drive spindle is checked, as this also has an influence on the remaining service life. By comparing the above-mentioned parameters, it is possible to check whether the fatigue limit load of the drive spindle has been exceeded.
In parallel to the more technical issues, the scenarios for business models were further developed. These support the machine manufacturer in particular in integrating the LongLife solution into his customer's service business in accordance with his wishes. According to the scenarios created for sample business models, a test station can be used, for example, as part of the maintenance work and be included directly as part of an existing maintenance contract. Alternatively, scenarios were considered where customers order the forecasts separately (forecasts as a service) or where they record the forecasts themselves with the help of a mobile test station. The latter may be of particular interest to end customers with their own maintenance staff in order to save costs and better schedule machine inspections. These results were transferred into a prototype web application that can be accessed via the LongLife website (https://longlife.uni-bremen.de).
The innovation of the project approach
The innovative approach combines a decentralised collection of relevant data, an AI-based learning forecast via a dedicated platform and the possibility to configure business models. This motivates value chain partners to apply the forecast and provide the necessary data. As a result, longer use of technical components is promoted, in line with the objectives of the “ReziProK” funding measure.
Publications
Final Report Part I (German, Mai 2023)
Final Report Part II (German, Mai 2023)
Interim Report (German, June 2020)
Project flyer of the funding measure (German / English) (March 2021)
The project flyers offer an insight into the contents and goals of the ReziProK projects and present first results in each case.
Project sheets of the funding measure (German) (August 2019)
The project sheets provide a brief overview of the individual projects and their goals.
Press release (German) (July 2020)
Newsletter article (German) (October 2022)
Contributions to the ReziProK Transfer Conference in June 2022
Poster (German) (June 2022)
Presentation (German) (June 2022)
Contributions to the ReziProK Kick-off event in December 2019
Poster No.1 - in German (December 2019)
Poster No.2 - in German (December 2019)
Presentation - in German (December 2019)
Picture credits: DESMA Schuhmaschinen GmbH; CoSynth GmbH & Co. KG; BIK Universität Bremen